Salvage Of The PRO-ASSIST III
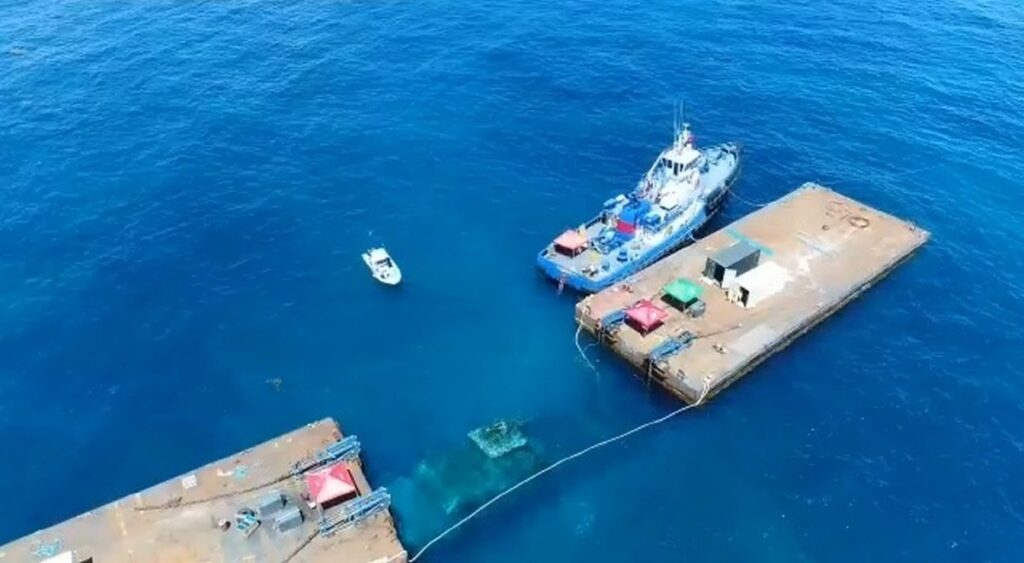
The Sinking
On the evening of December 24, 2020 (Christmas Eve), the U.S.-flagged tug “PRO-ASSIST III” sank in forty feet of water just off of Yabucoa, Puerto Rico. This forced her crew of three to abandon ship and be rescued by local fishermen. The vessel contained 1100 gallons of fuel and standard lube oil for a vessel of her size, with two main engines.
The tug was sinking and going down fast. It was Christmas Eve 2020 and the three-man crew of the U.S.-flagged tug, PRO-ASSIST III, had to abandon ship in 40 feet of water just off the coast of Yabucoa, Puerto Rico.
Call it a Christmas miracle, or the global goodwill of the maritime community, but local fishermen acted swiftly after being alerted to the casualty by American tugs dispatcher. They arrived to rescue the crew, just as the tug was slipping beneath the waves.
The PRO-ASSIST III contained 1,100 gallons of fuel and the standard amount of lube oil for a vessel of her size with two main engines. On Christmas Day, the tug’s owner, American Tugs Inc. (ATI), hired Key West Harbor Services / Nautilus Marine to consult and develop plans for fuel removal and vessel salvage.
The tug’s owner sent local divers 40 feet down to plug the fuel vents, assess the vessel’s condition, and record a video survey of the situation. The PRO-ASSIST III sank in a very rough area outside the Port of Yabucoa, where its position exposed the casualty to constant easterly trade winds. Fortunately, no sign of pollution was visible.
Preparation
Weeks of updates and conference calls followed, during which Key West Harbor Services submitted a Salvage Plan and received approval for its proposed refloat methodology.
The trade winds blew relentlessly and effectively closed any potential weather windows that would allow for the necessary salvage preparations.
Salvage Master Gordon Olson started to rethink the wisdom of refloating an older tug, and dove deep into the research of potential alternatives.
He formulated and received USCG approval for a new Salvage Plan that utilized four 250-ton chain pullers.
But first, Key West Harbor Services had to find those four 250-ton chain pullers. Luckily, there were four puller units for available on the West Coast of the U.S. After inspection and acquisition, the pullers were transported to the team’s yard in Florida. The puller units were loaded into seven containers, along with the required 3” chain and other equipment necessary for the project. The seven containers then headed for ATI’s yard in Guayama, Puerto Rico with a stop in Jacksonville, Florida.
Site Visit
Exactly seven months later, on July 25, 2021, the Salvage Master and Logistics Coordinator flew to Puerto Rico. They met ATI owner Pedro Rivera to fully assess the tug’s location and identify potential challenges.
Their first visit to the wreck site made those challenges abundantly clear, as the heavy seas necessitated changes to the Salvage Plan.
The team also met USCG Lieutenant Long and his team at ATI’s yard in Guayama, Puerto Rico, where the officials inspected the brackets and two barges – JMC 148 and JMC 144 – to be used in the operation.
Meanwhile ATI’s welders mounted the structural reinforcement brackets that would enable the barges to support the added load and stress of the chain pullers during lifting.
A Rough Start
The Key West Harbor Services crew arrived in Puerto Rico on August 15,2021 to begin the operation. Working alongside ATI’s crew, both teams began outfitting the two barges (with a Manitowoc 4100 onboard) with all the salvage gear.
Unfortunately, the crane suffered a major breakdown on Day 2 and the crew had to come up with a plan to hold the barges in place while the lifting rigging was installed.
They decided to anchor directly upwind and up-current to the casualty. Once the anchor line was stretched out, another line attached to the casualty would hold the salvage vessels in place. This would eliminate the need for spuds and a crane, and both barges would be sufficiently buoyant to support the weight of the sunken tug when lifted. The unforgiving weather conditions also prompted the salvage team to place the barges in line with each other rather than side by side.
The Best Laid Plans
Time had not been kind to the PRO-ASSIST III or the team working to raise her. Submerged and constantly battered by waves for eight months, the tug had moved 120 feet. It had been ground into the rocky sea bottom and the after house had been swept from its main deck.
The original salvage plan, developed when the stern was sitting proud on the bottom, would have allowed a lifting strap to be placed under one end of the vessel. The stern could be lifted and crews could insert the other lifting strap. Once both straps were in place, the vessel could have been lifted with a barge on each side.
But that wasn’t going to happen. The vessel was now buried, leaving no access under the starboard side.
Plans changed yet again and four holes had to be cut through the tug’s deck and out of bottom. Fortunately, the team was able to use both forward forepeak accesses for the deck holes of two of the connection points and another on an existing hatch in the stern.
Ocean Operations
After setting up the dive station and other salvage gear, the team began using the support tug “Alejandro” that ATI had provided. They tied a line to the sunken tug’s bits, then dropped an anchor in a position approved by the onsite marine biologist.
With the anchor in place and the moorings tested, the team could finally begin cutting holes for the lifting chains, a process that required approximately 5 to 6 trips offshore, weather permitting.
When the holes were complete, 2” chains were pre-rigged in all but one of the holes. The last hole (in the starboard stern) was still not accessible from the bottom. The first barge, JMC-144, was tied to the bow of the PRO-ASSIST III. The two bow chains were attached and the barge was left moored overnight.
The next day, the second barge, JMC-148, was moored to the stern of the PRO-ASSIST III. One chain was connected through the deck and around the shaft (for strength), then back over the deck to itself. The second chain was still not accessible, so the team tried to lift and move the vessel several times until there was access under the stern. Much to everyone’s surprise, the surveying diver found no starboard shaft.
This was not good.
The PROASSIST III needed to be transported 23 miles to the port of Guayama. There, it could be set down and the barges could be repositioned to enable a full refloat position.
Without the starboard shaft, the starboard chain could potentially rip through during the voyage. The only option was to place a loop around the starboard strut to relieve some pressure from the shell plating.
With the weather window closing, the last connection was made and the flotilla got underway at sundown on September 26, making 2 knots.
The flotilla traveled through the night, placing the vessels in the port of Guayama at noon the next day. The crew stored all the salvage gear, then returned the next day to reposition and let the PROASSIST III down on the harbor floor.
Once the barges were detached, the puller support brackets would be relocated on the sides of the barge so they could lift and refloat the PROASSIST III in between them.
On September 30, the Key West team departed for the U.S., while the ATI crew completed the needed modifications to the barges.
The Refloat of The PRO-ASSIST III
On October 19, the Salvage Team returned to prepare the barges for Phase 2, “The Refloat.” After a week of preparations, the Salvage Team raised the PRO-ASSIST III to the surface between the two barges with the relocated pullers. The vessels were moved to a dockside facility and an assessment was conducted.
The tug had endured an excessive amount of abuse in the nine months it spent on the ocean floor. While the bottom took the brunt of the damage, two-thirds of the house was swept away. When the dive team started patching, several cracks were found due to the wash boarding of the shell plating. This undoubtedly occurred when the vessel settled 6’ into the rock bottom. The dive team spent nearly two weeks patching the underwater portion of the tug. This included the missing starboard shaft, keel coolers, both sets of rudders, standard and flanking, the large holes the salvage team cut for the chains and the shell plating. Due to the unseaworthiness of the hull of the Pro Assist 3, it was decided to remove the hull from water and cut it into scrap.
Removal Of The Remains
After the ATI crews cut the vessel down to just the necessities. The hull was moved to the companies property and rolled out of the water and cut up.
In Conclusion
When Key West Harbor Services was asked to consult on the recovery of the PROASSIST III, the team did not realize the vessel was exposed to the trade winds on a nearly constant basis. They also discovered there is a short, two-month weather window in September and October. Without a pollution threat, Key West Harbor Services was able to time the recovery in those months.
Once the puller methodology was accepted and the engineering was done, the operations flowed fairly smoothly. The larger setback, including the loss of the crane, the ravaged condition of the vessel at its final position, the loss of the starboard shaft, the damage to the bottom by the rocky seafloor, and the restriction on anchor placement, were all overcome by the hard work and diligence of the Salvage Crew.
Due to the location and condition of the casualty, along with the mentioned and unmentioned setbacks, this project was a shining success. Although it was inherently more expensive than first thought, we believe it couldn’t have been executed in a more environmentally sound or professional manner for any less.